
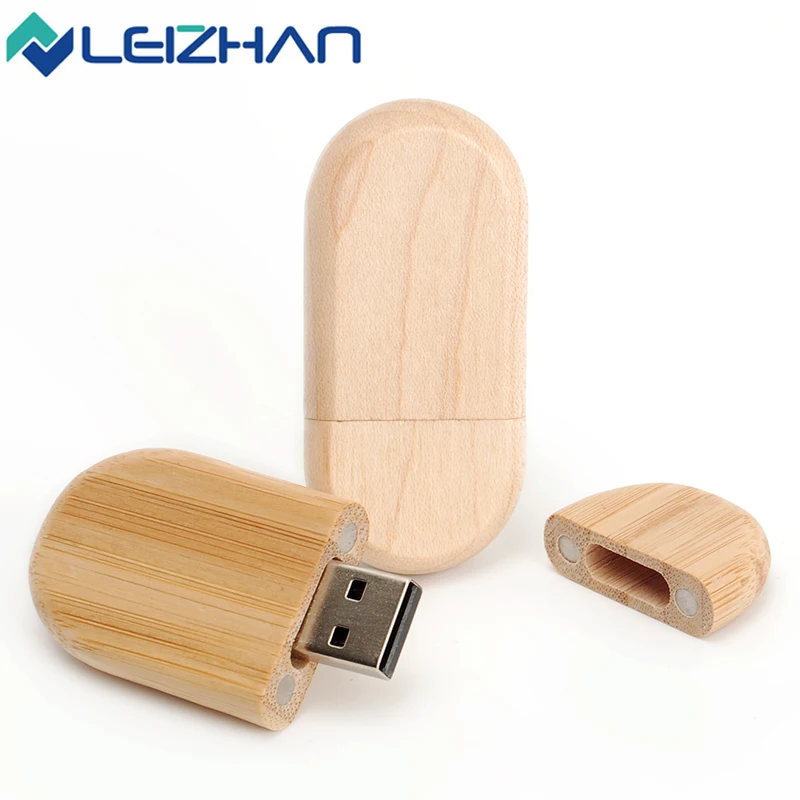
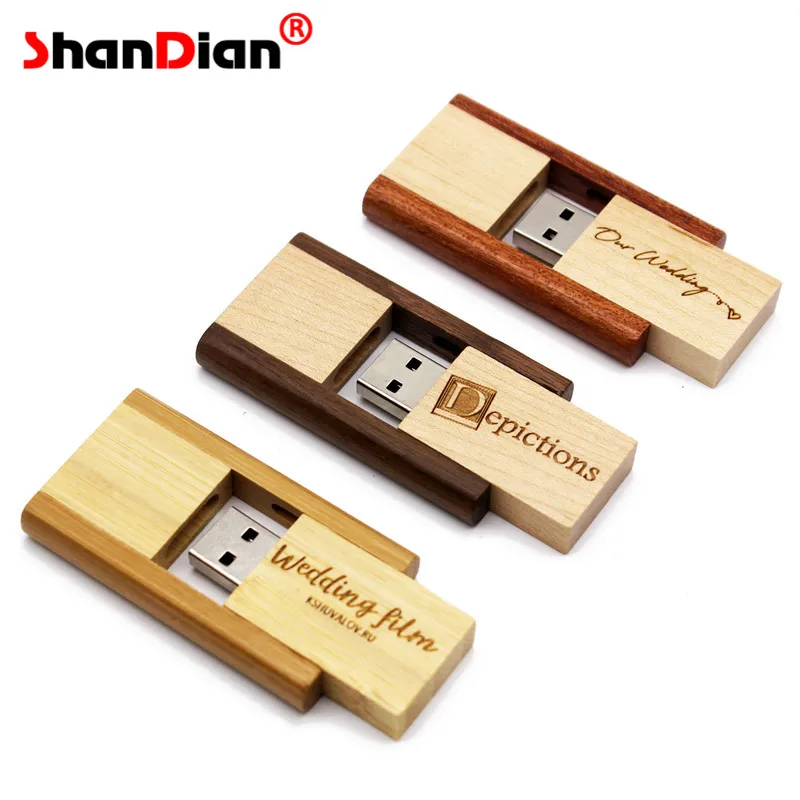

So where to start? At the root of determining the speed and feed for your project is knowing the chip load number. Here is an example of a clean cut with big chips – this is what you should aim for when you’re programming your feed rate. Fewer individual cuts at cooler temperatures prevents premature dulling of the bit (all of which saves time and money!).Ģ. Most of us hobby woodworkers don’t think much about maximizing bit life but CNC routers often run for many hours to complete a project. Large chips mean increased productivity, reduced heat buildup and therefore longer bit life. Your goal is to find a combination that produces the largest chip-the most efficient cut. So how do we determine the best feed and speed without this tactile feedback? The answer is with chip load calculations.ĭetermining the right speed and feed combination through chip load calculations can seem intimidating when learning to operate a CNC router but once you’re familiar with the basics it’s not that hard. The right feed and speed need to be programed into the toolpath before the machine is ever turned on. A CNC router also needs to run at an ideal feed rate and cutter speed but making changes while running isn’t generally an option. Changes can be made on the fly to obtain a cut of the best possible quality. If you smell burning wood from cutting you know to increase the feed rate and perhaps slow the router speed down. You can feel if the bit is chattering as it cuts, hear if the router is bogging down and you know to back off the feed rate and increase the bit speed. If you have spent time using handheld routers then you have developed an intuitive sense for what is the ideal feed rate and speed for the cutter. Understanding the importance of chip load calculations. Shown here is a close up of the CNC router cutting with small chips and dust flying – a symptom of poor cutting.
